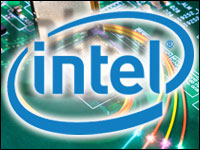
Intel has informed its shareholders that its fourth-quarter results will not match its earlier outlook. The reason: a global shortage of hard disk drives, due to flooding in Thailand earlier this year.
Now the company expects fourth-quarter revenue to be approximately US$13.7 billion, down from the previous estimate of roughly $14.7 billion.
These current challenges will carry into the first quarter, Intel spokesperson Jon Carvill told the E-Commerce Times. “The indication is that by the latter half of the first part of 2012 we should see a recovery.”
Bigger Picture
Earthquakes in Japan, New Zealand and Chile. A volcano eruption in Iceland. Hurricanes in the Gulf of Mexico. Flooding in southeast Asia. One doesn’t need to be a geologist to know that planet Earth is unstable, with a natural disaster all but certain to happen at some point during any given year.
Why then, does it seem that companies such as Intel fail to grasp this point and plan their supply chain operations accordingly? For indeed, it is not just Intel that will be hampered by the floods in Thailand for the next several months.
“The most notable industries affected by the Thailand floods have been technology and automotive, but the effects of these floods transcend industries to include energy, pharmaceutical, food distribution, construction and chemicals,” Drew Olson, manager at BDO Consulting, told the E-Commerce Times.
It does seem as though global manufacturers insist on learning the same supply chain lessons over and over gain, Gary Lynch, the global supply chain risk management leader for Marsh, told the E-Commerce Times. “These companies, though, are not stupid. They know very well the risks involved in having supply chains so closely intertwined.”
The Redundancy Challenge
There are many reasons companies are unable to build more redundancy into their operations, Lynch said.
For starters, supply chain software still does not provide enough visibility into a company’s operations. The software does provide transparency, but only to a certain point and only in a certain sphere — such as financial risk or operational risk. It doesn’t tell a company that, say, the unavailability of a $1.50 piston-engine part manufactured by a tier- three supplier in Japan could throw an entire production schedule out of whack.
That, in fact, is what happened after the earthquake in Japan earlier this year. Several automobile manufacturers were blindsided when the part became scarce.
“Because it is a commodity part, a lot of companies didn’t see it as important enough to track,” Lynch said.
When the scarcity becomes apparent, companies go into Darwinist mode, he continued. “In situations like this, you have many companies trying to grab as much of a supply as they can when they realize it is scarce. You also have not just the manufacturing community monitoring and acting on these trends, but also the financial community — such as hedge funds, which don’t want to have positions in an industry that is suddenly going to have supply problems.”
After earthquake in Japan, the second phone call Lynch received was from a hedge fund.
Too Many Parts to Track?
Another problem for companies is that products now tend to consist of many different components. One automobile line can have 5,000 suppliers, he noted.
Factor in tier-two and tier-three suppliers, and the challenge of tracking supply becomes almost insurmountable, Rose Kelly-Falls, the SVP of supply chain risk at Rapid Ratings, told the E-Commerce Times. “A lot of companies just don’t know who their tier-two suppliers are for this reason. It is just too much to track.”
Then, when natural disaster does strike, gathering information, especially in developing economies, can be exceedingly difficult, Kelly-Falls said. “With the flooding in Thailand, it has taken weeks in some cases to get people on the phone.”
This is not an operating environment where contingency plans are easy to execute, BDO’s Olson said. “In order to keep up with demand, companies will need to airfreight goods rather than use more traditional shipping methods. This is more costly, but poses less risk to the supply chain and overall operations. ”
With all of the challenges, the fact that global companies are able to operate at the level that they do is a wonder, Lynch said.
Certainly this is a position that Intel maintains, even as it pulls back on its guidance due to its own supply chain glitch. “I would say the PC industry has been very resilient,” said Carvill.
Social Media
See all Social Media